Taming the Flames: Simulating Sprinklers in Fire Dynamics Simulator (FDS)
Introduction
Fire sprinklers are a critical component of fire safety systems, designed to detect and suppress fires quickly, protecting lives and property. Simulating their behavior in a fire environment using tools like Fire Dynamics Simulator (FDS) can provide valuable insights for design and safety analysis. This post will delve into how you can effectively model sprinklers in FDS, exploring both direct particle-based representation and a more advanced approach using a precursor simulation to improve accuracy.
Method 1: The Straightforward Approach with PART
The most common way to model sprinklers in FDS is by using the PART
namelist, specifically by defining a set of spray particles. Here’s how it works:
- Creating a
PART
: You define aPART
namelist with properties that mimic water droplets: size, density, temperature, and velocity. These particles are then injected into the simulation at a specified location when a certain condition is met. - Sprinkler Activation: You can trigger the injection of these particles based on a variety of conditions, the most common being temperature at a specific location (
TR
, i.e., the activation temperature of the sprinkler head). You can define different activation conditions based on your needs. - Spray Pattern: The
PART
namelist allows you to define the angle and velocity of the sprayed droplets, enabling you to simulate different spray patterns. You may need to explore or consult sprinkler technical manuals for appropriate droplet sizes and spray angles. - Key Parameters to consider in the
PART
namelist:PART_ID
: A unique identifier for your particle.MASS_RATE
: The mass flow rate of the water from the sprinkler.DIAMETER
: The diameter of the water droplets.VELOCITY
: The initial velocity of the water droplets.SPREAD_ANGLE
: The angle of the spray pattern.TEMP
: The initial temperature of the water.TR
: The activation temperature of the sprinkler head.XYZ
: The location of the sprinkler head.VEL_VECT
: Direction of the velocity.PART_ID
: Particle ID that is generated by the flow source (e.g.PART_ID='SPRINKLER'
).
This method is relatively straightforward and suitable for many applications. However, it relies on a pre-defined activation temperature and doesn’t explicitly account for the thermal inertia of the sprinkler head itself.
Method 2: Precursor Simulation for More Realistic Activation Timing
To enhance the accuracy of your sprinkler simulation, you can employ a more sophisticated two-step process, leveraging the power of DEVC
(Device) objects:
- Precursor Simulation: Characterizing Sprinkler Activation Time
- Setup: Run a preliminary simulation of the fire without any sprinkler particles. In this simulation, you simulate the full heat release rate (HRR) curve of your fire source.
- Adding a
DEVC
object: In your simulation, define aDEVC
object representing the sprinkler head. This device will measure the temperature at the specific location of the sprinkler. - Analyzing Results: Monitor the temperature measured by the
DEVC
object. Record the simulation time at which theDEVC
reading reaches the activation temperature of the sprinkler head (e.g. 75°C). This is the approximate activation time of the sprinkler, which we’ll use in the subsequent simulation.
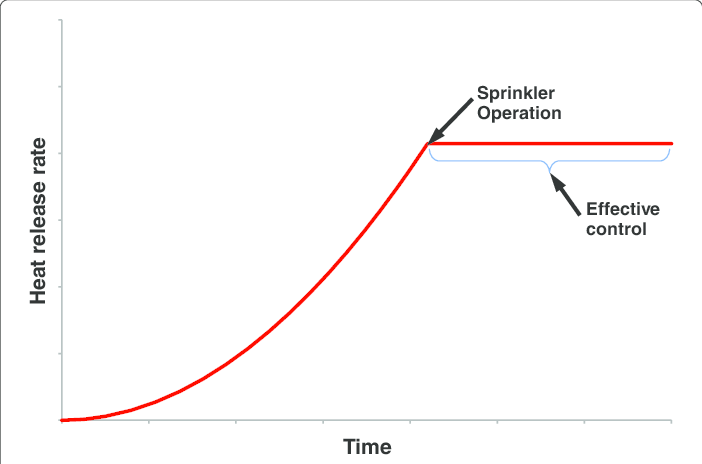
- Main Simulation: Limiting the HRR Curve
- Adjust the HRR Curve: In this subsequent simulation, we will replicate the original setup, including the same fire source. However, the difference is that now, you will modify the fire’s HRR curve. Instead of allowing it to increase according to the original fire growth curve, you’ll set a limit on its growth. The time of the maximum HRR will be equivalent to the sprinkler activation time we extracted in the precursor simulation. After this activation time, the fire will no longer increase its intensity.
Why Use the Precursor Method?
- More Accurate Activation: The precursor simulation method accounts for the heat transfer from the fire to the sprinkler head, providing a more realistic activation time than just using a static temperature.
- Reduced Computational Load: By limiting the growth of the fire’s HRR, you can avoid the simulation to reach the peak HRR, which may also be unachievable.
- Improved Accuracy: By simulating a more realistic fire scenario including sprinkler activation, you improve the accuracy of your results.
Important Considerations
- Meshing: Ensure your computational grid is sufficiently fine to accurately model the fire, the sprinkler spray, and the interaction between them.
- Droplet Size: Use appropriate droplet sizes in your
PART
namelist that match the sprinkler you’re simulating. - Validation: Whenever possible, compare your FDS simulations with experimental results or available data to validate the accuracy of your model.
- Computational Cost: The precursor method adds to the computational time, but it’s often worth it for increased accuracy in certain cases.
Conclusion
Simulating sprinklers in FDS can be achieved using different methods. The PART namelist is the simplest, but the precursor method, with the help of DEVC
, offers a more accurate representation of the sprinkler activation and its effect on fire behavior. By understanding these methods, you can effectively utilize FDS to enhance fire safety design and analysis. Remember to always validate your simulations and consider the limitations of your models.
Note: Please consult the FDS user guide for a complete description of all parameters and syntax.
Let me know if you’d like any specific part expanded further!
CloudHPC is a HPC provider to run engineering simulations on the cloud. CloudHPC provides from 1 to 224 vCPUs for each process in several configuration of HPC infrastructure - both multi-thread and multi-core. Current software ranges includes several CAE, CFD, FEA, FEM software among which OpenFOAM, FDS, Blender and several others.
New users benefit of a FREE trial of 300 vCPU/Hours to be used on the platform in order to test the platform, all each features and verify if it is suitable for their needs